“Rubber tubing” is a term that refers to hollow synthetic and natural rubber channels, or flow lines, that transfer or dispense liquids and gases. With their varying chemical compositions, rubber tubings’ characteristics are quite diverse, which is advantageous for professionals who wish to engage tubing. Industries and applications such as these include: food and beverage processing, medicine and surgery, commercial heating and cooling, lawn and garden care, Petro-chemical extraction, sanitation and more. Read More…
We are rubber tubing experts, and we have been since our founding in 1954. We serve the entire world with quality tubing products right from the heart of Pennsylvania.
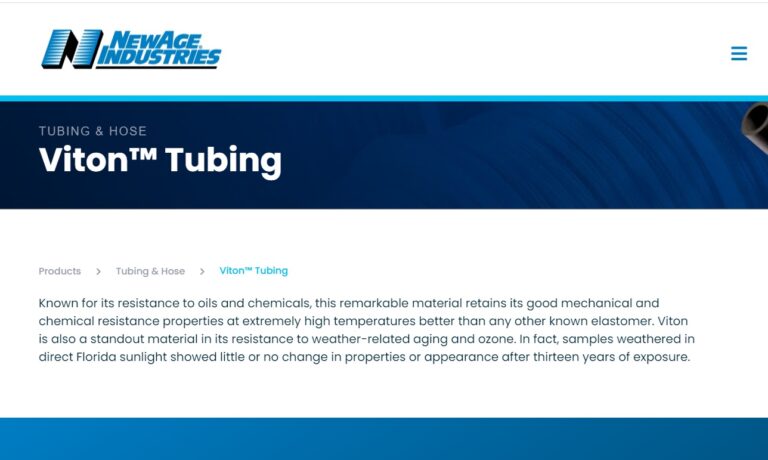
As the largest in-house pure gum inventory carrier in the U.S., Atlantic Rubber Company has cost-effective and resilient rubber tubing. We carry a variety of materials so that we can make the best product for your needs.
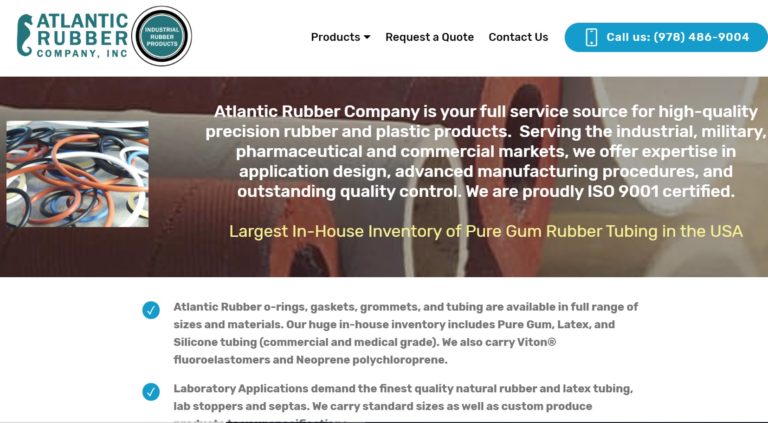
At Kent Rubber Supply Co., we specialize in providing high-quality rubber tubing solutions to meet the diverse needs of our customers. With decades of experience in the industry, we take pride in offering a comprehensive selection of durable, reliable, and customizable rubber tubing products. Our tubing is designed to perform in a wide range of applications, including industrial, commercial, and...
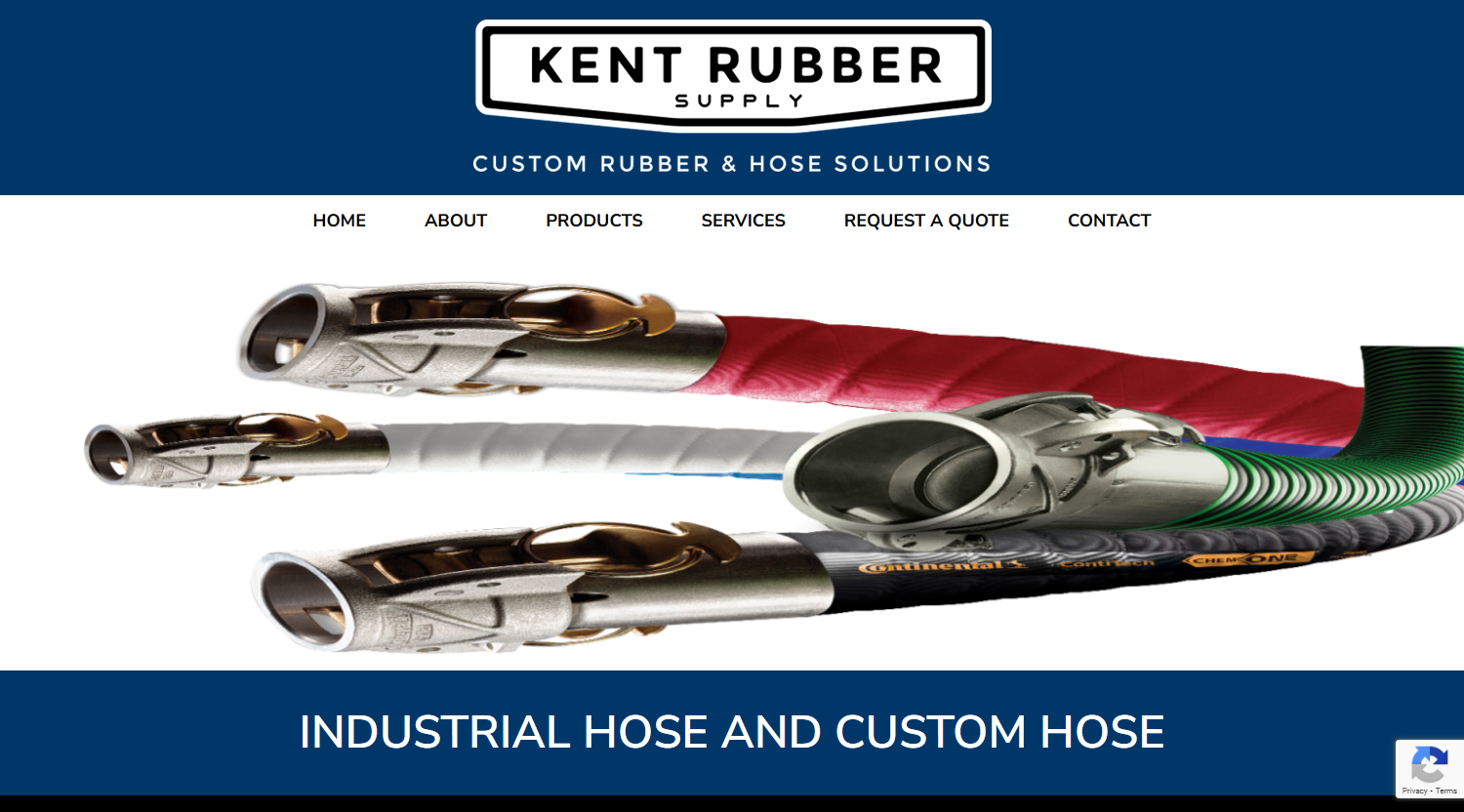
Manufacturer of standard and custom rubber tubing. Made of EPDM, neoprene, nitrile, dense, recovery sponge rubber and silicone compounds. Secondary processes such as die cutting, notching, and glue splicing are offered.
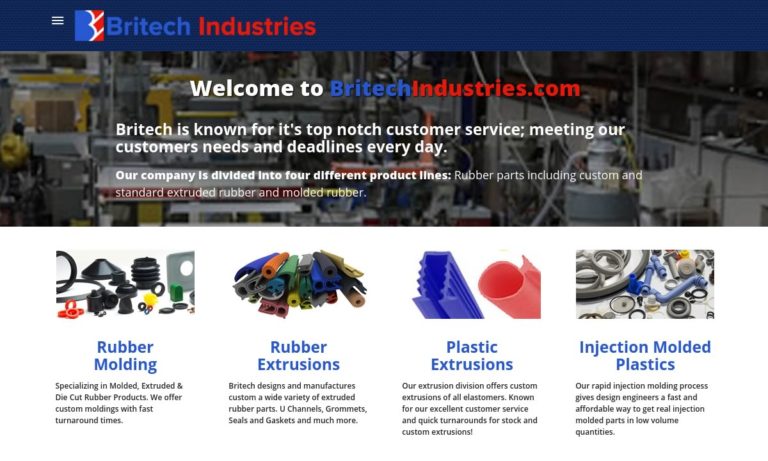
Established in 1986, GSH Industries supplies plastic, aluminum and rubber tubing to an array of industries including automotive, consumer, marine and electrical.
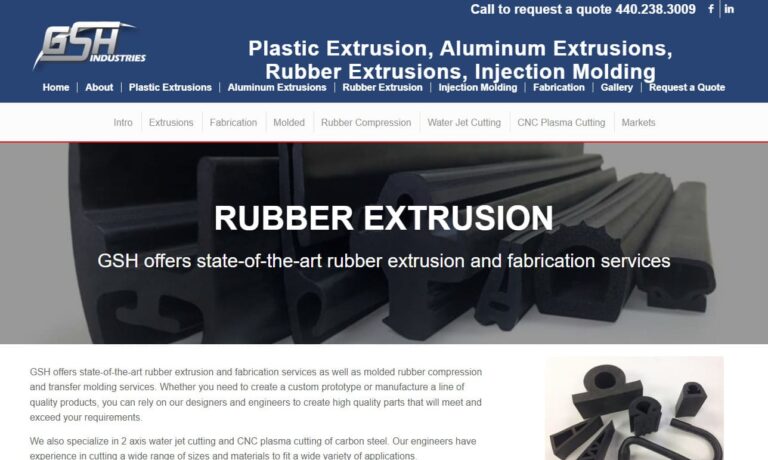
At Flexaust Industrial, we specialize in providing high-quality rubber tubing solutions that meet the diverse needs of industries worldwide. Our team is dedicated to manufacturing durable and flexible tubing that stands up to the toughest applications. We pride ourselves on delivering products that offer exceptional performance in demanding environments, from industrial to commercial sectors.
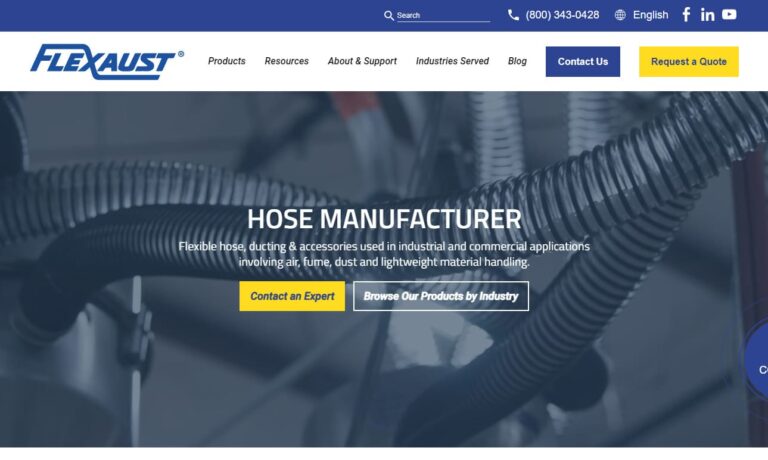
More Rubber Tubing Manufacturers
The History of Rubber Tubing
Rubber tubing has been utilized since the 1800s. Notably, in the mid-1800s, various inventors developed rubber tympanostomy tubes to relieve fluid accumulation in the middle ear. This includes Lincke’s rubber tube and Ádám Politzer’s hard rubber drain.
Initially, rubber tubing was made from pure gum rubber, or natural rubber. For several decades, Latex tubing dominated the market. However, in the 1980s, allergists identified latex allergies in a small portion of the population. This led to a reduction in latex usage, particularly in gloves, which were replaced with non-latex alternatives.
Long before this discovery, manufacturers had already started producing synthetic rubbers. In 1909, scientists at Bayer developed the first viable synthetic rubber, aiming to create a more efficient and cost-effective material for the rapidly growing automobile industry. This innovation quickly expanded to other applications, including rubber tubing. Synthetic rubber types like butyl rubber tubing gained significance during both World War I and World War II.
In 1957, DuPont (formerly E.I. du Pont de Nemours & Company) developed Viton, a fluoroelastomer that enabled aerospace engineers to produce tubing with enhanced corrosion resistance, chemical inertness, and wide temperature tolerance.
Currently, rubber tubing is available in a diverse array of shapes, sizes, and materials, offering numerous possibilities for professionals and end-users globally.
Rubber Tubing Production Process
Rubber, a versatile material, is created through a process that involves the extraction of latex from plants and its subsequent treatment to enhance its properties. This treated latex can be used to produce various types of rubber tubing, each suited for different applications. Examples of rubber tubing materials include natural latex, neoprene, silicone, vinyl rubber, EPDM, and Viton.
Material Preparation
The material can be prepared through either latex extraction and treatment, or through rubber synthesization. Natural rubber is harvested from plants like the Pará tree through a process similar to tapping a maple tree for syrup. The latex is collected in containers and then mixed with various substances to enhance its properties. One common enhancement is vulcanization, where latex is treated with heat and sulfur to increase its strength. Other treatments can make latex rubber sterile, conductive, spark-resistant, explosion-proof, reinforced, extra flexible, elastic, or resilient.
Material can also be prepared through rubber synthesization. In this process, manufacturers blend various compounds to create custom rubber materials. This involves precise formulation and mixing techniques to achieve desired properties and performance characteristics.
Extrusion
To fabricate rubber tubing, manufacturers employ the rubber extrusion process. This involves an extruder that pushes uncured rubber through a specialized die, molding the material into the required cross-sectional shape. This method ensures precision and consistency in the final product.
Secondary Processing
Upon extruding the tubing, manufacturers often subject it to various finishing and secondary processes to enhance its functionality and appearance. These processes encompass a broad spectrum of techniques, including cutting, curing, coating, drilling, and labeling. Each of these steps is meticulously executed to ensure the final product meets the highest standards of quality and performance.
Considerations and Customization
Manufacturers design rubber tubing based on application specifications such as environment (moisture, temperature, pressure) and the fluid being conveyed. They produce tubing in various diameters and thicknesses, from a few thousandths of an inch to several inches, with diverse properties, colors, shapes, and attachments. Tubing may connect to instruments, tools, or additional tubing using hose barbs, fittings, gaskets, grommets, and other attachments.
Types of Rubber Tubing
Latex Tubing
The latex utilized in latex tubing is sourced from the Pará rubber tree and various other plant species, classifying it as a natural rubber. This material is highly esteemed for its exceptional flexibility and chemical inertness. Due to these properties, latex is frequently employed in the production ofconductive rubber tubing, surgical tubing, rubber hoses, and black rubber tubing. However, latex is also recognized as a relatively common allergen, which limits its applicability in certain scenarios. In such cases, synthetic rubber tubing, such as neoprene, is preferred as an alternative.
Neoprene Tubing
Neoprene tubing is a highly versatile material characterized by its hypoallergenic properties, buoyancy, elasticity, and lightweight nature. Additionally, it offers remarkable resistance to chemicals and abrasion. These attributes make neoprene tubing an ideal choice for a broad range of applications, including the transportation of liquids and gases. Moreover, it serves as an effective protective covering for wires and cables, ensuring durability and reliability in various industrial and commercial settings.
PVC Rubber Tubing
PVC, or vinyl rubber tubing, boasts several advantageous properties, including resistance to solvents, acids, and alkalis, as well as excellent insulative capabilities. It is available in both rigid and flexible forms, and can be obtained in clear PVC or a wide range of colors. This versatile tubing is suitable for numerous applications, such as food and beverage processing, brewing, drainage, pool cleaning, wastewater management, protective insulation, and pharmaceutical processing.
Silicone Tubing
Silicone tubing, also known as silicone rubber tubing, is characterized by its elasticity, pliability, and flexibility. It features a smooth surface and exhibits exceptional resistance to heat, weather, and water.
EPDM Tubing
EPDM, another robust synthetic rubber tubing, is derived from ethylene propylene diene monomers. This elastomer is predominantly utilized in industrial rubber and automotive applications due to its superior performance and durability.
Viton Tubing
viton tubing, a relatively recent innovation, was developed in 1957 specifically for the aerospace industry. As the world’s first synthesized fluoroelastomer, Viton represents a significant advancement in high-performance rubber technology. This specialized material is designed to withstand substances and conditions that traditional rubber tubing cannot, making it exceptionally durable and versatile for demanding applications.
Microbore Tubing
Microbore tubing, utilized for intravenous lines in medical applications, is a specialized form of tubing designed to ensure the seamless delivery of sensitive liquids. This tubing boasts robust structural integrity, enabling it to maintain its shape and support itself without compromising the fluid flow. Additionally, microbore tubing is characterized by its sterility, ultra-smooth surface, and inert properties, making it an ideal choice for precise and safe medical procedures.
Metal Rubber Tubing
A recent advancement in material science is the introduction of metal rubber tubing. This innovative tubing exhibits remarkable resilience, as it can endure freezing temperatures, significant stretching, and exposure to various chemicals, all while maintaining its original form without any damage. Composed of polymers integrated with metal ions, this tubing combines flexibility with lightweight properties, making it an exceptional choice for a wide range of applications.
Conductive Rubber Tubing
Conductive rubber tubing, designed to prevent static electricity buildup and shield electronic equipment from electromagnetic and radio frequency interference, includes varieties such as conductive silicone rubber tubing and conductive latex rubber tubing.
Sterilized Rubber Tubing
Sterilized rubber tubing undergoes a meticulous process to ensure it is free from any contaminants. This can involve chemical treatments that meticulously cleanse the material, gamma irradiation that penetrates deeply to eliminate microorganisms, or exposure to dry heat which methodically eradicates any lingering germs. Each method guarantees that the rubber tubing is safe and hygienic, ready for use in sensitive environments where sterility is paramount.
Thermoplastic Rubber Tubing
Thermoplastic rubber tubing, crafted from various types of thermoplastic rubber, is renowned for its elasticity, allowing it to flex and stretch while reliably returning to its original shape. This material exhibits a robust combination of rigidity and durability, making it highly resistant to abrasion. Additionally, it offers the advantage of being recyclable.
Surgical Tubing
Surgical tubing is meticulously designed to meet the specific demands of medical environments and to be compatible with the human body. To facilitate unobstructed fluid passage, it is typically manufactured with thin walls.
Black Rubber Tubing
Black rubber tubing is particularly effective at absorbing heat compared to clear tubing, making it ideal for insulation and heat retention applications. A notable variant, black nitrile rubber tubing, offers exceptional resistance to vegetable oils, mineral oils, and acids, enhancing its suitability for various industrial uses.
Hose Rubber Tubing
Hose rubber tubing consists of rubber tubing reinforced by rigid rubber or fine metal wires. These reinforcements enable the hose assembly to maintain its shape, even when not in use. Rubber hoses are frequently utilized as garden hoses, while industrial hoses serve various purposes, such as material handling.
Foam Tubing
Foam tubing is a solid material, making it unsuitable for fluid conveyance. Instead, it is primarily utilized for cushioning, insulation, or as a gripping surface for various products, such as handles.
Advantages of Rubber Tubing
Rubber tubing offers numerous benefits to its users, regardless of the rubber type. It is affordable, generally costing less than plastic or metal tubing, with prices often starting below $10. Even with customization, rubber tubing remains cost-effective compared to metal options.
Rubber tubing is highly versatile, allowing manufacturers to meet a wide range of aesthetic and functional requirements. It is also easy to transport and store due to its ability to be rolled or folded. Maintenance is straightforward, as detailed in our Proper Care for Rubber Tubing section. Additionally, rubber tubing’s flexibility ensures it can navigate complex paths within facilities while maintaining consistent fluid flow.
Proper Care for Rubber Tubing
To achieve optimal performance, it is essential to maintain your rubber tubing properly. For guidance on effective maintenance practices, please continue reading.
Handling
The initial aspect to consider is the proper handling of your tubing. Given the inherently soft and flexible nature of rubber tubing, it is susceptible to tearing, abrasion, and other forms of damage if not handled with care. Even with protective layers, it remains essential to avoid rough handling. Exercise caution and treat the tubing with care to maintain its integrity.
When transporting the tubing, ensure it does not drag on the ground. Proper storage is equally important; keep it elevated and shielded from moisture and dust to prolong its lifespan. Additionally, avoid tying the tubing in knots, crushing it, or placing any weight on it. Such practices will help preserve its functionality and durability.
Usage
Always use tubing for its intended application. Avoid using it for alternative flows, as this can lead to corrosion, contamination from rubber leaching, or even tube failure. For additional applications, consult your manufacturer for appropriate tubing.
Cleaning and Inspection
The final step in maintaining rubber tubing involves cleaning and inspection. Consult your supplier for the recommended cleaning frequency and establish a routine accordingly. Generally, the tubing should be cleaned with a cloth and soapy water, followed by air drying. Ensure to clean any attachments as well. Before cleaning, inspect the tubing for damage and leaks. For wide leaks, either replace the tubing or cut out the damaged section and reconnect the remaining parts with a connector.
Rubber Tubing Uses in the Concrete Sector
Rubber products play a crucial role in the construction industry, particularly in material transportation and operational tasks. Common rubber components include hoses, belts, mountings, rollers, sheets, flooring, tires, adhesives, and sealants. However rubber is specifically useful in the concrete industry.
Concrete is composed of cement, water, aggregates, and additives. It can be produced on-site or at ready-mixed batch plants, depending on the construction site’s location and the required volume. On-site production is ideal for distant locations and large projects needing a continuous supply of concrete. In contrast, ready-mixed batch plants are suitable for supplying multiple smaller sites nearby. Both methods utilize rubber tubing for handling wet and dry materials essential for constructing foundations, flooring, and exterior surfaces in commercial and residential buildings. The specific applications of rubber tubing in the concrete sector include:
Powder Discharge
Rubber tubing is used to transfer dry materials such as cement, sand, and concrete powder via compressed air or gravity. These tubings are essential for loading and unloading dry bulk powders to and from silos, storage bins, and trucks. Known for their resilience and durability in harsh environments, rubber materials are well-suited for the concrete industry. The tubings are crafted from abrasion-resistant materials to endure the high-abrasion effects of dry powders.
Dust Collection Ducts
Transferring dry materials to central mixers generates dust. Moisture levels, silt content, size distribution, concrete mix, production rates, wind speed, and direction influence dust emission rates. Collecting particulate emissions reduces pollution and worker hazards. Cement particles can cause skin and eye irritation and respiratory illnesses. Concrete batch plants use rubber tubing in dust collection systems.
Concrete Placement
Transferring dry materials to central mixers generates dust. Moisture levels, silt content, size distribution, concrete mix, production rates, wind speed, and direction influence dust emission rates. Collecting particulate emissions reduces pollution and worker hazards. Cement particles can cause skin and eye irritation and respiratory illnesses. Concrete batch plants use rubber tubing in dust collection systems.
Rubber Tubing Standards
Standards for rubber tubing are essential to ensure product safety and reliability across various industries, including medical, automotive, industrial, and aerospace. These standards help manufacturers produce tubing that meets specific performance criteria, thereby reducing the risk of accidents or failures. In the United States, organizations such as ASTM International and ANSI develop consensus-based standards that cover critical aspects of rubber tubing, such as material properties, dimensions, testing methods, and safety requirements.
Standards encompass various types of rubber tubing, including explosion-proof variants designed for hazardous environments. These standards establish criteria ensuring the tubing can endure extreme conditions such as high pressures, temperatures, or chemical exposures without risk of explosion or combustion.
Non-compliance with these standards can have serious repercussions. Users may encounter accidents, product failures, or legal liabilities, while manufacturers risk legal action, reputational damage, and financial losses from product recalls or lawsuits if their products do not meet the necessary standards.
Standards apply to different types of rubber tubing, including those designed to be explosion-proof for use in hazardous environments. These guidelines specify the requirements that ensure the tubing can withstand extreme conditions like high pressures, temperatures, or chemical exposures, without posing risks of explosion or combustion.
Ignoring these standards can lead to significant consequences. For users, non-compliant rubber tubing can result in accidents, equipment failures, or legal issues. For manufacturers, failing to meet standards can lead to legal action, damage to their reputation, and financial losses due to product recalls or lawsuits.
Adhering to established standards is crucial for both consumers and manufacturers. For consumers, it ensures confidence in the safety and performance of rubber tubing, knowing it has undergone rigorous testing and meets industry-recognized criteria. For manufacturers, compliance with standards streamlines production, enhances product quality, and expands market opportunities. It also provides a competitive advantage by demonstrating a commitment to high-quality, reliable products. In the United States, organizations like ASTM and ANSI play a vital role in developing and maintaining these standards. Overall, adherence to standards ensures safety, reliability, and performance, benefiting both users and manufacturers by minimizing risks and enhancing reputations.
Choosing the Right Rubber Tubing Manufacturer
For the best results when purchasing rubber tubing, use our directory to compare multiple manufacturers. Each manufacturer has a profile page detailing their expertise and capabilities, along with a contact form for inquiries or quotes. Utilize our patented website previewer to quickly assess each company’s specialties. Finally, use our streamlined RFQ form to contact several manufacturers simultaneously.